Abstract: This paper discusses a simple, low-cost, high-efficiency dual-lens objective system with a simplified illumination system. Compared with the current six-lens extreme ultraviolet (EUV) projection lens system, the output power requirement of the EUV light source can be reduced by 1/10. Based on a processing speed of 100 wafers per hour, the required EUV light source power is only 20 watts. The newly designed projection lens can achieve 0.2 NA (20 mm field) and 0.3 NA (10 mm field), and can be assembled into a cylindrical device similar to the deep ultraviolet (DUV) projection lens system, with excellent mechanical stability and easier assembly and maintenance. The extreme ultraviolet light is introduced in front of the mask through two narrow cylindrical mirrors located on both sides of the diffraction cone, providing average normal illumination and reducing the three-dimensional effects of the lithography mask. The simplified illumination system provides symmetrical four-pole off-axis illumination, bypassing the central shielding, improving spatial resolution, and also achieving Kohler illumination. The theoretical resolution limit is 24 nm (20 mm field of view), with an image reduction factor of x5 and an object-image distance (OID) of 2000 mm. After using a curved mask, the object-image distance can be greatly reduced to (OID) 1500 mm, with a resolution of 16 nm (10 mm field of view). It will be suitable for the production of small-sized chips for mobile terminal applications and the latest chiplet chip technology.
1. Introduction
Over the past few decades, people have been committed to extensive research and development and a large amount of investment in extreme ultraviolet lithography technology. Key components such as high-precision multi-layer mirrors with a diameter of nearly 1 meter and high-power EUV light sources have been successfully developed. Mass production lithography machines with a numerical aperture (NA) of 0.33 are now in use. However, for EUV lithography technology to be widely accepted as a reliable tool for mass production, it must be economically feasible. Therefore, the cost issue needs to be addressed. Although Moore's Law still applies, it must be remembered that the resources on Earth are limited. Therefore, we must strive to achieve sustainable development goals. The chip industry should avoid excessive consumption of electricity and water resources when developing the next generation of products.
Advertisement
This paper aims to find a cost-effective solution that meets performance requirements within a reasonable time frame using existing technology. Therefore, we focus on low numerical aperture (low NA) lithography technology with an inline dual-lens configuration, as shown in Figure 1. This approach helps to reduce costs and save electricity.
EUV lithography mirrors absorb more than 30% of the EUV power with each reflection. The current exposure tool has six reflective mirrors in the projection lens system and four reflective mirrors in the illumination lens system, so the power transmission from the EUV source to the wafer is quite low. In contrast, the simplified illuminator's dual-mirror projector proposed in this paper uses two tandem reflective mirrors, and the power transmission efficiency will be greatly improved.
The energy efficiency of the scheme is increased by 13 times, reducing the power consumption of the EUV lithography system by 92%. This will reduce the power consumption of the lithography machine system from about 1 megawatt to 80 kilowatts. In addition, the cooling water flow of the laser light source system will also be greatly reduced. The required extreme ultraviolet light power during the intermediate focus is 20 W, and the throughput of each tool is 100 wafers per hour. The design of the EUV light source is simplified, reducing investment and maintenance costs, and improving reliability. At this power level, a thin film window can be installed around the focus (IF) position close to the EUV collector in the illumination system, similar to the thin film on the mask, to prevent plasma source debris and protect expensive masks and mirrors. Due to the weakness of the EUV light source, the scanning speed of existing EUV tools is usually slower than that of optical scanners. However, by using the system proposed in this paper, we can increase the actual output power of EUV to the wafer, thereby increasing the scanning speed and improving productivity.
The surface roughness of the projection lens will affect the image quality. For this reason, we have carried out a lot of technical research and development to achieve ultra-precision surfaces. In particular, the mid-frequency roughness within the micron range will severely affect the image contrast, which is the same as the fog phenomenon in nature. In synchrotron radiation light source equipment, the surface of the mirror is often contaminated with carbon, which also leads to a decrease in image contrast. The surface cleanliness of the EUV lithography system will be much better, but we also need to be careful about carbon contamination. It is recommended to reduce the number of reflective mirrors in the lens system to obtain high-contrast images and maintain them for a long time.It should also be noted that the infrared light transmitted through optical components by the CO2 laser of the EUV light source heats the wafer, which can affect the overlay control of the overlay precision. In the system studied in this paper, the EUV light source power and the CO2 driving laser power were reduced by 10 times, thereby eliminating this problem.
At a lower numerical aperture (NA) value, optical aberration correction is easier because the light rays run near the axis. Only two aspheric mirrors are needed to cover a relatively wide field of view. Optical simulation confirms that NA 0.2 will provide a 20 mm size field of view for a 2-meter high objective lens system. Compared with the immersion lithography machine ArFi, the low NA EUV has a higher resolution because its wavelength is much shorter, only 13.5 nanometers, which is 15 times shorter than ArF's 193 nanometers. The critical dimension or resolution is determined by the Abbe equation:
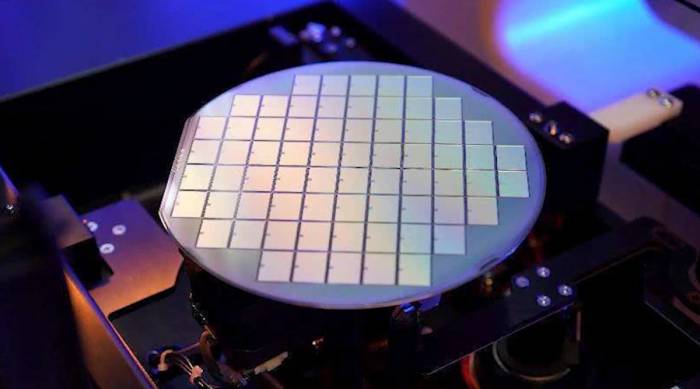
\[ \text{Resolution} = k1 \cdot \frac{\lambda}{NA} \]
where \( k1 \) represents the process coefficient, \( \lambda \) represents the wavelength, and NA represents the numerical aperture. The spatial resolution is determined in both cases:
\[ k1 = 0.36 \text{ for EUV} \]
\[ k1 = 0.27 \text{ for ArFi} \]
Using this low NA value EUV, it is possible to achieve single-shot patterning at a half-pitch of 24 nm. Please refer to the later section on EUV with \( k1 = 0.35 \) in the ultraviolet light.
Another important issue is the depth of focus (DOF), which is defined as follows.
\[ \text{DOF} = \frac{k2 \cdot \lambda}{NA^2} \]
Substituting equation (2) into equation (43), we can derive a dimensionless relationship:
\[ \text{Dimensionless DOF} = \frac{k2}{k1^2} \cdot \frac{\lambda}{\text{NA}} \]This equation tells us that a lower numerical aperture always provides a greater depth of field (DOF). There are two scenarios:
In both scenarios, we assume that k2 = 1. It is clear that low numerical aperture (NA) extreme ultraviolet (EUV) light has an advantage for a larger DOF. Additionally, compared to traditional EUV lithography objective systems that use off-axis illumination on the photomask, the embedded objective does not exhibit the characteristic image variations around the focus due to the need for illumination uniformity. This eliminates image position errors caused by photomask unevenness. Therefore, using low NA EUV simplifies the requirements for reticle and wafer flatness as well as focus control. It also makes it easier to implement curved masks, which will be discussed in later sections.
Axisymmetric optical devices provide uniform image contrast around the axis, simplifying source mask co-optimization (SMO). Traditional quadrupole illumination is sufficient. Moreover, the maximum reflection angle of the AM2 dual-objective system is only 5.5 degrees from the surface normal. This results in minimal asymmetric pupil halo, no polarization dependence, and no phase changes associated with multilayer coatings.
At extreme ultraviolet wavelengths, quantum mechanical effects must be considered, especially the higher photon energy may reduce patterning effects, which is known as stochastic effects. The formula for calculating photon energy is:
In both scenarios:
The energy of EUV photons is 14 times that of ArF, so under the same absorbed energy, the number of photon ionization events in the photoresist is 14 times less. Due to the random Poisson distribution, this leads to worse LER (line edge roughness). Defects caused by stochastic phenomena limit the stability of the lithography process. We must remember that the contact failure rate required for large-scale production of logic circuits must be less than 3 x 10^-11. Currently, many R&D teams are working to understand the relevant mechanisms and have proposed new photoresist materials to overcome these challenges. However, these solutions may still take some time to emerge. In the meantime, it is recommended to use a projection objective with a lower NA and adopt wider line spacing. Lower-cost EUV lithography technology may achieve narrower linewidths using multiple patterning techniques. It is also important that the dual-mirror projection objective system can provide more photons, helping to reduce statistical stochastic noise issues.
As shown in Figure 1, the dual-mirror projection objective is installed in a tube similar to that of an ultraviolet lithography lens. Ultra-precision mirrors are encapsulated inside the tube, forming a single unit with the advantages of mechanical stability, easy assembly, calibration, and replacement, as well as good sealing and dust resistance. Therefore, the capital investment and maintenance costs are lower, and reliability is higher.
2. Optical devices for aberration correction2.1 Image Error Correction in Dual Mirror Configuration with Equal Radii
EUV lithography technology requires a plane field image disperser that uses only mirrors.
The Petzval and regular principles are the core principles of a flat field projector. In a dual mirror configuration,
where \( R \) is the mirror curvature. The most basic configuration of a dual mirror projection objective should consist of positive and negative power mirrors, specifically a concave mirror and a convex mirror with the same radius. This is known as the "equal radius" configuration, as shown in Figure 2. When the distance between the two mirrors is \( L = 0.86 R \), the object (OBJ) on the secondary mirror \( M2 \) will be projected onto the image (IMG) on the first mirror \( M1 \), thereby correcting the third-order spherical aberration.
To create a functional projector, we need to adjust the mirror curvature, pulling the vertices (OBJ and IMG) outward through the central hole. This will disrupt the Petzval-sum rule, leading to aberrations. Aspherical mirrors must be introduced to correct the aberrations, but due to the limited number of free aspherical parameters (only two mirrors are available), the numerical aperture and field of view are restricted.
The equal radius structure is named MET: In 2008, R. M. Hudyma and R. Soufli carefully studied it as an extreme ultraviolet projection objective. The MET with a numerical aperture (NA) of 0.3 was designed to demonstrate 30-nanometer half-pitch imaging. One of the designs assumed a virtual transmission mask and an embedded projection objective, with a configuration similar to Figure 1, but the illumination must be provided through the virtual transmission mask. Aspherical mirrors are used to correct the aberrations, resulting in a residual root mean square (rms) wavefront error of 0.027λ. The projector has a compact structure with an object-image distance (OID) of 276 millimeters. However, due to its limited field of view of only 0.6 millimeters x 0.2 millimeters, it is not suitable for use as a lithography tool.
In 2004, MET demonstrated 30-nanometer equal-line space printing using the synchrotron radiation facility at Berkeley Advanced Light Source. This success indicates that the dual mirror projection objective system has great potential.
2.2 Expanding the Field of ViewTo enlarge the magnetic field size, it is necessary to increase the length of the projection objective lens. Assuming the tool height is within the maximum acceptable size range in an actual semiconductor factory:
To maintain the Petzval-sum rule, the position of mirror M2 must be close enough to the wafer. Assuming the gap between the lens and the wafer is the same as the ArF immersion, it is recommended that the gap between the wafer and the M2 mirror body should be 5 millimeters. To ensure the mirror body remains rigid, the distance between the wafer and the M2 surface should be greater than 40-50 millimeters. As shown in the figure below, two mirrors with very close curvatures (difference within 0.3%) can achieve a wider field of view.
The OpTaLix simulator predicts a field of view of 20 millimeters at NA = 0.2, covering a full mask field of 100 millimeters. The image reduction factor is 1/5. We can also introduce a curved mask to eliminate residual field curvature errors, thus shortening the tool height and reducing wavefront errors, which will be discussed later.
2.3 Practical design of a dual-mirror projector
The optical ray simulation results are shown in Figure 3, where AM1 and AM2 are axially symmetric aspheric mirrors. To guide the light into the projection objective lens, a spacious area is needed to accommodate the cylindrical mirror between AM1 mirror and the mask. This leads to a magnification factor of x5, equivalent to MET, instead of the standard magnification factor of x4. The size of the mask scanning area is 100 millimeters (20 millimeters x 5), which matches the current mask design of 104 millimeters (26 millimeters x 4). The simulation results at NA 0.2 are summarized in Table-1 and Table-2.
Table 1. Dual-mirror projector parameter table.Table-2: Aspheric Design Parameters (OpTaLix Output)
The simulation assumes a perfect mirror surface with a reflectivity of 100%. In reality, the mirror surface is composed of multiple reflective layers, and the reflection is caused by wave interference between these layers, which can produce amplitude and phase differences as the angle of reflection changes. We need to further carefully simulate, including multi-layer reflective layers, which will lead to changes in the aspheric curvature, although this change is very small. In fact, we need to use an interferometer to measure the quality of the mirror under visible light wavelengths.
The wafer side is telecentric, but the mask side is not. Therefore, the chief ray is inclined; it is inclined by 1.6 degrees at the edge of the field of view (~50 mm/2000 mm radians). Considering the semi-angle of the diffraction cone (NA/5 = 0.04 radians = 2.4 degrees), the maximum reflection angle of the multi-layer reflective layer coating at the mask edge is 4 degrees. This angle is less than the 12-degree cutoff angle of the molybdenum/silicon multi-layer coating, so the contrast loss is minimal. Defocus will still cause pattern shift, and a 100 nm wafer height error will cause a 3 nm shift at the edge of the field. This kind of shift is acceptable.
Please note that all light from different fields intersects at the focal plane, forming a diffraction spot that represents the Fourier space. The light must pass through the central hole on both reflective mirrors, which blocks the central part of the diffraction signal. The impact of the central obstruction at the focal plane can be estimated separately using Fourier analysis (see later).
Wavefront aberration and spot diagram. The wavefront error is small at a small image height, but at the edge of the image field, the wavefront error reaches the limit of 0.05 times the wavelength due to residual aberration. Due to the lower NA value, the Strehl ratio at the edge of the field of view is still very high (0.991). We must pay attention that the Strehl ratio is estimated without central obstruction and coaxial illumination. If we adopt oblique illumination, the high-frequency components will start to pass through the projection lens, and the resolution will be improved, but there will be obvious aberrations. Fortunately, the wavefront error in Figure 4 is axisymmetric (actually cylindrically symmetric), and the phase difference between the first-order Bragg diffraction from the narrowest pattern and the off-axis quadruple illumination decreases, which means it can effectively reduce aberrations. Further detailed research is also needed.
The wavefront error along the beam height, with the vertical scale being 0.05 times the ultraviolet light wavelength (0.05*13.5 nanometers). At the edge of the scanning field (y = 10 mm), the Strehl ratio is as high as 0.991, leading to a diffraction-limited spot with NA 0.2.
Spot diagram on the wafer. The simulated output is the spot on the mask, and based on this spot, the spot on the wafer side can be estimated, taking into account the 1/5 image reduction factor.2.4 Surface Masking Options
Due to the limited number of mirrors, the projected image is not completely flat and curved. As shown in Figure 4, the best focus point varies with the height of the field of view, leading to wavefront errors. If we introduce a surface mask as shown in Figure 6, we can compensate for the y-field curvature. The curvature of the mask we designed matches the Petzval field curvature, as shown below:
\[ R_{\text{curve}} = \frac{2n}{1 + \sqrt{1 - \lambda R_{\text{Petzval}}^2}} \]
where \( R_{\text{curve}} \) is the theoretical optimal radius of the surface mask. In practice, the spherical aberration compensation radius predicted by OpTaLix is slightly smaller.
By introducing a surface mask, the degree of freedom of the design parameters is increased, that is, we can reduce the tool height, or increase the thickness of the AM2 mirror. Table 3 summarizes the design parameters when using a surface mask, which can meet the requirement of a Strehl ratio greater than 0.99. Compared with the light mask width, the bending radius is large, and the bending amount is relatively small, there are no mechanical problems on the light mask, and the lateral pattern shift can be integrated into the pattern design. We make the flat light mask as usual, and then bend it when the light mask is installed on the scanner designed with a curved chuck. Further discussion is needed with the light mask developers and pattern designers.
Figure 6. The concept of a surface mask compensating for the Y-field curvature.
Table 3: Design parameters of the surface mask.
2.5 DistortionIt is well known that distortion can cause the image of a lithographic machine to become blurry. In a double-mirror projector, the magnification decreases as the axial distance increases, leading to a characteristic "barrel" distortion, which can be described mathematically:
The unit of distortion Cd is %. r is the ideal axial position, and r' is the distorted position. As shown in Figure 7, due to radial distortion, a point on the mask is projected as a curved trajectory (dashed line) in a linear scanning motion. As discussed later, we used a double line field separated from the center. Since a smaller gap will reduce image smearing, we minimize the gap to two scanning widths that are tangent to each other on the axis.
As shown in Figure 7, the distortion effect moves point A to point A', and point B on the edge to point B'. Based on the height difference between A' and B', we can determine the smear offset on the wafer. Using formulas (13a) and (13b), where m is the image magnification factor m = 5. When we use w = 2.5 mm and y0 = 50 mm on the mask, the smear width on the wafer becomes 9 nm. In the central part, the curved trajectory is more parallel to the scanning motion, and the root mean square value becomes about one-third: 3 nm. This will be an acceptable level when generating a feature size of 24 nm half-pitch.
Figure 7. Image blurring caused by radial distortion during scanning motion.
3. Central Masking
The design of the double-mirror combined projection objective inevitably leads to a central masking problem due to the central beam hole on the mirror. The key issue is how to eliminate the "forbidden imaging spacing." It is impossible to completely avoid this problem solely by the projector design, but we can effectively reduce the impact on the projection pattern. There are three strategies to address this issue:
(1) Minimize the beam hole as much as possible.
(2) Optimize off-axis illumination.
(3) Optimize the partial coherence factor.Central Beam Hole. In this paper, to distinguish between the shielding coefficient and the partial coherence coefficient, we use the Greek capital letter for the shielding coefficient and the lowercase letter for the partial coherence coefficient.
The central hole is designed to pass a beam with an NA value of 0.2, with a 2 mm gap around the edge of the beam. The shielding in AM1 is usually less than AM2, so we only discuss AM2.
The normalized hole size (shielding coefficient) is represented as Σ = 1, indicating the diffraction cone (mirror diameter). The NA value is lower, so the beam hole and horizontal blur are smaller. We made an AM2 secondary mirror near the wafer to maintain the Petzval-sum rule. This decision also helps to reduce the size of the beam hole.
We introduced quadrupole illumination, which can bypass the central shielding. The logical pattern is mainly composed of vertical and horizontal lines, and its diffraction is distributed along the horizontal and vertical axes, as shown in Figure 12. If the spacing of the four times the light spot (0-order diffraction) in the horizontal and vertical directions is greater than the size of the shield, the diffraction will not be shielded by the shielding hole. In the current design, it is obviously satisfied.
In the special case of the interlaced contact hole, the diffraction pattern should have a 60-degree rotational symmetry, so there is still an opportunity for the shielded area to enter the forbidden distance interval. We can save some of the shielded points through partial coherence sources. Since the partial coherence factor is greater than the shielding rate, that is, σx = 0.25 > Σx = 0.13, the diffusion width of the diffraction spot will be greater than the width of the central hole, so the lost diffraction spot will be saved, as shown in Figures 12 and 14.
Further research is also needed, including the use of computational lithography technology for source mask optimization (SMO) and optical proximity correction (OPC).
Beam shielding on the main mirror and the secondary mirror. The design of the beam hole conforms to the edge of the beam with NA 0.2, with a 2 mm gap around the beam. The three circles represent the diffraction cones of the axis and the two field edges.
In order to avoid the central shielding and improve spatial resolution, EUV light is introduced through two narrow cylindrical mirrors located on both sides of the diffraction light cone in front of the mask. This provides a uniform illumination field, reducing the three-dimensional effect of the mask. The simplified illumination system provides symmetrical quadrupole off-axis illumination, bypassing the central shielding, improving spatial resolution, and also achieving Kohler illumination. To avoid the blocking diffraction of the cylindrical mirror, the double-line field concept was introduced. Technical details are currently in the design stage and will be introduced in another paper in the near future.4. Partially Coherent Light Sources
When using point light sources for illumination, the frequency components near the edges are abruptly cut off by the aperture (hard edge truncation), which usually leads to knife-edge diffraction effects in the image. To avoid this issue, optical lithography typically employs partially coherent light sources.
The definition of the partial coherence factor is as follows.
In the case of a point light source, σ = 0.
In traditional ultraviolet lithography, quadrupole illumination often uses a partial coherence factor of 0.2, and EUV should ideally use the same value. It is worth noting that partial illumination also mitigates the impact of central shielding. The size of the shield in the X direction is Σx = 0.13, so partially coherent light compensates for the hole problem.
We will discuss the size of the light source in the X and Y directions separately. First, let's discuss the X direction. The scanning field is very narrow: 2.5 millimeters wide, so the natural angular spread of the extreme ultraviolet plasma light source meets the required angular spread. As shown in Figure 10, we assume that the collection angle for each segment mirror in the X direction is 1 radian. The diameter of the tin plasma is about 100 um, from which we cut out a 50 um wide plasma, then magnify it 50 times through the illuminator, and transmit it to the mask in the form of a 2.5 mm wide line field. Since the phase space area is preserved through linear optics (the same as the emission conservation law in particle accelerators), the angular divergence is adiabatically reduced by 1/50, so the angular spread on the mask becomes 20 mrad. Compared with the entrance pupil diameter of 2 x NA/m = 2 x 0.2/5 = 80 mrad, the partial coherence factor becomes σx = 20/80 = 0.25, which meets the required value.
Phase space distribution from the extreme ultraviolet light source to the mask. (a) The diameter of the plasma is about 100 micrometers, from which we cut out a width of 50 micrometers. (b) The light source size is magnified 50 times by the illuminator and transmitted to the mask in the form of a 2.5 millimeter wide line field. The angular divergence is adiabatically reduced by 1/50. (c) The reception between the two cylindrical mirrors and the collimator cuts off the phase space. 60% of the photon flux can reach the wafer. The dashed line represents the illumination.In the y-direction, the illumination device expands the light to a line width of 100 millimeters to cover the size of the mask. However, this results in a minimal angular divergence, which does not meet the required partial coherence. To increase the divergence in the y-direction, a "grating mirror" can be introduced into the illumination device. The "grating mirror" was originally introduced by Henry N. Chapman and Keith A. Nugent in 1999 for curved scanning fields. The mirror has periodic undulations that can mix light and effectively increase the partial coherence factor without losing a large amount of light.
The off-axis quadrupole illumination mode of the focal plane is shown, considering the partial coherence factors σx = 0.25, σy = 0.2. The shadows of the two cylindrical mirrors are blurred, and part of the illumination and diffraction light can pass through, so there should be a 10-15% margin on the mirrors to correct for aberrations.
The four illumination light points are symmetrically distributed near the pupil size, at a 45-degree angle to the axis. The available resolution is determined by the frequency width, that is, 2NA cos(45) = 1.4NA. Therefore, the critical size becomes:
Off-axis quadrupole illumination mode of the focal plane. The off-axis angle is taken to meet the pupil size of NA, and the frequency span becomes 1.4 NA. The shadows of the cylindrical mirrors are blurred, and part of the illumination and diffraction can pass through, so a 10-15% margin should be reserved on the mirrors, that is, the aberration correction required when NA is 0.22 should cover the diffraction.
5. Imaging capability under quadrupole illumination
This section presents preliminary results of the imaging analysis, illustrating the impact of central obstruction and the shadows of two cylindrical mirrors under quadrupole illumination. Further optimization work is needed to study various logic patterns, the spacing of the two cylindrical mirrors, and the partial coherence and pupil filling factors. This issue is related to photons lost in the line scanning slit and central hole, and these photon losses will be reflected in the required EUV light source power. The flexibility of the illumination scheme in this proposal is somewhat limited. However, we have enough EUV power on the projector to optimize (including the pupil filling factor) the reasonable contrast of various logic patterns, which is sufficient for our purpose.
The Fresnel number F is defined as F = a^2 / Lλ, where a is the characteristic size, L is the distance from the object, and λ is the incident wavelength. For a 1-micrometer field of logic patterns, only 1 millimeter away from the mask surface, F = 0.07 << 1, so diffraction becomes a Fraunhofer mechanism, that is, we can use Fourier transform to deal with diffraction. For nano patterns, F is always very small, in the Fresnel and near-field state.
Diffraction propagates from AM2 to AM1, and between AM1 and AM2, light from different field heights intersects on the focal plane, producing a Fourier pattern of the mask image. As shown in Figure 8, the three circles represent the diffraction cones on the axis and at the two field edges. Compared with the diameter, the displacement is relatively small, so we use the diffraction at the field center to approximate the imaging capability. As shown in Figure 8, the central obstruction rate of AM2 is higher than that of AM1, so we estimate the obstruction rate of AM2.
The FFT analysis of the 27 nm HP half-pitch vertical line is shown. From left to right are the test pattern, the diffraction on the focal plane, the overlapping diffraction aligned with the origin 0, and the back FFT aerial image. The second row is the unobstructed (no hole) case. The cylindrical mirror in front of the mask blocks part of the diffraction, and the shadow is not completely black. This is due to the non-zero light source size, that is, the 50 nm-mrad phase space (Δx, Δx') (see Figure 10), which makes the shadow of the mirror blurred.27nm half-pitch HP vertical line FFT fast Fourier analysis. The images from left to right are the test pattern, the focal plane diffraction, the overlapping diffraction aligned with the origin 0 times, and the back FFT fast Fourier space image. The second line is the unobstructed (no hole) situation.
It is worth noting that the strong diffraction forms a rectangle surrounding the central hole. Therefore, the power directed to the central hole is small. As a result, the impact of the central obstruction is relatively small in this case. This point will not change on the horizontal line.
The intensity on both sides of the vertical line. It can be seen that the contrast does not weaken due to the central obstruction, but is slightly enhanced. This can be explained as follows. The loss of the signal in the hole is equivalent to adding a signal with a phase shift of 180 degrees, which enhances the contrast in a similar way to the phase shift mask.
35 nm staggered contact hole FFT fast Fourier analysis. From left to right are the test pattern, the focal plane diffraction, the overlapping diffraction aligned with the origin 0 times, and the back FFT space image. The second line is the unobstructed (no hole) situation. As shown in Figure 15, a certain amount of diffraction energy enters the hole, so the contrast is reduced. As discussed by Jo Finders and others, three or six pole off-axis illumination is suitable for imaging with higher resolution and better contrast. However, the system proposed in this paper is based on four-pole illumination, which may not be the best choice for imaging of the staggered contact hole array. Nevertheless, the system is still simple and economically feasible.
35 nm staggered contact hole FFT fast Fourier analysis. From left to right are the test pattern, the focal plane diffraction, the overlapping diffraction aligned with the origin 0 times, and the back FFT aerial image. The second line is the unobstructed (no hole) situation.Translation of the provided text into English:
Intensity Curve of the Central Light Spot
6. Summary and Comments
The main features of the novel EUV lithography technology studied in this paper are:
Low power consumption, expected to reach less than 1/10 of the existing EUV lithography equipment power consumption (reducing the 1 megawatt power consumption of current EUV lithography systems to 100 kilowatts)
Simpler EUV light source hardware, lower cost, and longer service life.
A simple dual-mirror projection objective reduces investment costs and makes the design more reliable.
Easier to maintain.
Adopting a narrow line approach.
The ability to perform multiple patterning with a single exposure capability of 24 nm HP half-pitch (0.2NA, 20 mm field of light) is a reasonable strategy. It should be noted that the lithography process cost will be lower.
0.3 NA (16 nm HP, 10 mm field of light) can be achieved with a curved mask. The 10 mm x 26 mm field of light size is suitable for mobile applications.The article translates to English as follows:
Perfectly integrated with the "chiplet" design.
The author suggests conducting a principle verification experiment as soon as possible, possibly using a half-scale model, that is, an OID of 1000 millimeters, 0.2 NA, and a 10-millimeter light field (with or without a curved mask).
Comments