In the post-Moore era, the semiconductor industry is facing a tough battle for "yield." As chips become increasingly complex and the density of transistors multiplies, the difficulty of yield management in chip manufacturing also grows exponentially, especially for wafer fabs pursuing advanced processes, which could become a fatal weakness.
Yield: The Lifeline of Semiconductor Factories
Yield is the core competitiveness of semiconductor factories and is also known as the "lifeline" of semiconductor factories.
The semiconductor yield rate is the percentage of the actual number of chips produced compared to the maximum number of chips (integrated circuits) on a wafer. In other words, yield is the ratio of the actual production quantity to the total input quantity. The higher the yield rate, the higher the production efficiency, and yield directly affects costs and capacity utilization. Therefore, improving yield is very important in the semiconductor industry. At the same time, yield is also one of the important indicators for assessing the competitiveness of enterprises, directly reflecting the stability of the manufacturing process and the reliability of product quality.
Advertisement
In the field of logic chips, following the guidance of Moore's Law, the most advanced process that can currently achieve mass production is 3 nanometers. In this field, TSMC and Samsung are the two major players, and the two have engaged in fierce competition in the 3nm battle.
Samsung announced the mass production of 3nm in June 2022, a few months earlier than TSMC. Samsung is the first company in the industry to introduce the gate-all-around (GAA) process at 3nm, while TSMC still uses the FinFET transistor architecture. However, Samsung has encountered a Waterloo in yield. Although Samsung recently denied the news reported by the Korean media ZDNet Korea that Samsung's 3nm yield is below 20%, due to yield issues, Samsung has indeed lost a large number of customers.
Google's Tensor processor was outsourced to Samsung Electronics' foundry department before the fourth generation, but from the fifth generation that introduced the 3nm process, it turned to TSMC. Samsung's own Exynos 2500 chip is also troubled by yield issues. On June 25, the well-known analyst Ming-Chi Kuo commented on the social dynamic on the X (formerly Twitter) platform, stating that due to the lower-than-expected yield of Samsung's self-developed Exynos 2500 processor 3nm chip, it cannot be shipped.
It is expected that this year, Fabless companies and IT giants, including smartphones, servers, and artificial intelligence, will start to use 3nm as the main process. In the face of the important assessment index of yield, due to TSMC's leading advantage, it is expected to obtain most of the 3nm orders from major manufacturers, which may further widen the market share gap between TSMC and Samsung Electronics.However, even TSMC, currently its 3nm process yield is not high compared to the previous generation. TSMC is also actively improving the yield of 3nm.
The issue of low yield is not limited to the field of logic chips, and memory chips are also facing the same challenge. Generative AI is consuming a large number of HBM memory chips, but yield has always been one of the obstacles to the mass production of Nvidia GPU chips. According to Reuters, Samsung's high-bandwidth memory HBM3 chip production yield is about 10% to 20%, while SK Hynix's HBM3 yield can reach 60% to 70%. In the traditional DRAM memory, Samsung's fifth-generation 10-nanometer (1b) process DRAM yield has not reached the industry's general target of 80% to 90%, forcing Samsung to set up a special working group last month to solve this problem.
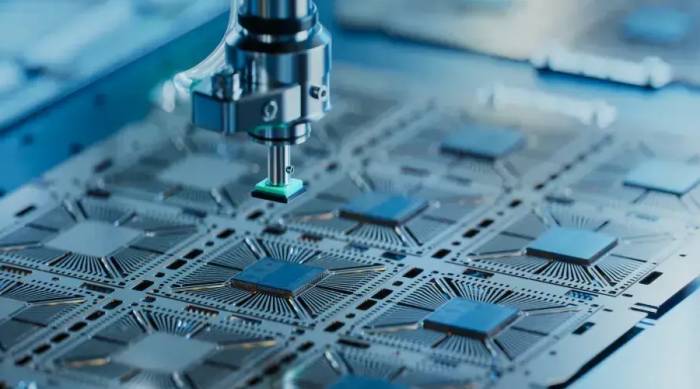
And next, generative AI is still rolling forward, and the demand for chip computing power is bottomless. In order to obtain AI chips with higher performance and higher computing power:
On the one hand, logic manufacturers are actively breaking through to the 2nm process, TSMC and Samsung are currently planning to start mass production of 2nm in 2025, while also focusing on advanced packaging technologies such as FOPLP (fan-out panel-level packaging);
On the other hand, memory manufacturers are also heavily investing in the research and development of the next generation of HBM (i.e., HBM4), and various advanced technologies are also being considered, such as hybrid bonding.
It can be imagined that the yield will become a major difficulty at that time. According to the "Korean Economic Daily", SK Hynix is recruiting dozens of positions related to HBM. In its recruitment advertisements, it is hoped that chip experts can improve the yield of HBM chips by improving the foundry process and testing logic chips.
Low yield is a common problem faced by semiconductor manufacturers and is also a bottleneck restricting the development of the chip industry. From an economic perspective, improving chip yield can also be seen as another continuation of Moore's Law. How to improve yield under the background of continuous introduction of new technologies has become a key issue that every semiconductor manufacturer must solve.
Why is it so difficult to improve yield?
To improve yield, we must first clarify what causes low yield? There are many factors that affect the yield of semiconductor manufacturing, but they are nothing more than "people, machines, materials, methods, environment, and measurement".Specifically:
People: The technical level and operational standards of operators directly affect the stability of the production process.
Machines: The precision and stability of semiconductor manufacturing equipment directly affect the microstructure and size of the chips.
Materials: The purity and consistency of raw materials affect the quality of the chips.
Methods: The control of process parameters and operational accuracy are crucial for yield.
Environment: Environmental factors in the production workshop can affect the manufacturing process of the chips.
Measurement: The performance of testing equipment and testing methods affect the accuracy of yield assessment.
However, as the chip process continues to advance towards more advanced processes, factors affecting yield are even more "elusive":
On the one hand, the progress of the process involves an increase in the number of process steps and types of materials, and the types of defects on the chips are becoming more and more diverse, and the causes of defects are complex, making them difficult to analyze and troubleshoot. On the other hand, the continuous introduction of new processes, new materials, and new equipment also brings new challenges to yield improvement. In addition, improving yield requires a significant investment of funds and manpower, including R&D investment, equipment investment, and talent training. Moreover, some advanced detection and analysis methods also require high costs.
This is also why for every step forward in the industry, the yield becomes increasingly difficult to improve.In order to improve yield rates, the industry is racking its brains.
To enhance the yield rates in semiconductor manufacturing, all parties in the industry are sparing no effort to optimize and innovate in various aspects.
Reducing contaminants: The complex multi-step processes of semiconductor manufacturing involve the use of a large amount of gases and solutions, which serve as the "lifeblood" of the industry. The purity and reliability of these gases/liquids largely determine the performance and yield rates of semiconductor devices. According to estimates by industry insiders, yield losses due to contamination can be as high as 50%.
Contamination control is a crucial part of the semiconductor manufacturing process. If contaminants such as particles and impurities are present in gases and solutions, it can lead to defects in the chips, reducing yield rates and even causing chip scrap. Therefore, how to effectively remove these contaminants and ensure the purity of the "lifeblood" is a major challenge faced by semiconductor manufacturing.
To meet the urgent demand of the industry for advanced processes and the challenge of improving yield rates, Pall Corporation, a global expert in filtration, separation, and purification solutions, has continued to increase investment in recent years. Last year, Pall's Gaskleen and Profile II dual production lines at its Beijing factory were officially put into production and launched. In June of this year, Pall announced the start of production at its Singapore factory, adding two important filter product lines: Litho lithography and WET wet chemical, which can provide strong support for the manufacturing of logic and memory chips at the current advanced process nodes.
Pall Beijing Gas Filtration Products
Pall can provide a full range of semiconductor filters, including CMP filters, lithography filters, gas filters, gas purification systems, ultra-pure water filters, wet etching filters, etc. These powerful filters have advanced nano-level impurity interception capabilities, which can remove particles, impurities and other contaminants at different key processes, ensuring the high quality and high yield rate of chips. In addition, efficient filtration technology can reduce the damage of contaminants to equipment, extend the service life of equipment, and reduce maintenance costs.
Process optimization: Process optimization is the cornerstone of improving yield rates. By continuously improving the manufacturing process, improving the precision and controllability of the production process, and reducing the occurrence of defects. For example, adopting EUV lithography technology, 3D packaging/Chiplet/CoWos and other advanced packaging technologies and other advanced processes.
Introducing AI and big data analysis technology: In the semiconductor manufacturing process, there are a large number of process parameters and production data. Leveraging emerging technologies such as AI and big data to achieve higher yield rates and less input has become a consensus in the industry. The upgrade of data management in semiconductor factories to intelligent is an inevitable trend.Engineering Intelligence (EI), Computer Integrated Manufacturing (CIM), Manufacturing Execution Systems (MES), and other industrial software are essential tools in semiconductor manufacturing. With the integration of AI and big data technologies, these software solutions are continuously being upgraded to provide more intelligent functions for semiconductor factories. Under the intelligent manufacturing paradigm, the production process becomes more transparent and controllable, significantly enhancing production efficiency and product quality.
Automation Upgrade: Reducing the human operation link and lowering the defect rate caused by human operation errors is an important means of improving yield. The introduction of Automated Guided Vehicles (AGVs), overhead cranes, and Autonomous Mobile Robots (AMRs) is accelerating the semiconductor manufacturing towards a new era of intelligent manufacturing. The application of automated equipment can effectively reduce the human operation link, liberating workers from heavy physical labor and repetitive work, thereby reducing the defect rate caused by human operation errors and improving production efficiency and product quality.
It can be seen that improving the yield rate in semiconductor manufacturing is a complex system engineering task, requiring semiconductor manufacturers to continuously innovate and improve from various aspects such as materials, processes, equipment, and management to effectively reduce the defect rate and enhance product competitiveness.
Conclusion
Today, yield improvement has become one of the core drivers of the development of the semiconductor industry. We also see filter manufacturers like Pall actively striving to expand production and build factories, continuously improving the level of filtration technology and capacity, to ensure the application of advanced processes and the improvement of yield.
It is believed that through the collaboration of the entire industry chain and continuous efforts to overcome difficulties, the semiconductor industry will be able to continuously improve the level of yield, promote high-quality development of the industry, and contribute more to global economic growth.
Comments