Recently, NXP and GlobalFoundries announced plans to invest $7.8 billion in building a new chip factory in Singapore, which is expected to be operational by 2027. Once operational, the factory will be able to produce chips on a scale of over 50,000 silicon wafers per month, focusing on the field of analog and mixed-signal chips.
The collaboration between NXP and GlobalFoundries, in addition to selling these chips to the automotive, industrial, consumer hardware, and mobile device sectors, is more thought-provoking in terms of the trend of IDM giants and wafer foundries joining forces to build factories.
In fact, in recent years, there has been a trend of IDM manufacturers and wafer foundries joining hands to build factories.
For example, in 2023, TSMC partnered with Bosch, Infineon, and NXP, three European chip companies, to jointly establish the European Semiconductor Manufacturing Company (ESMC) and build a wafer factory.
In July 2022, STMicroelectronics and GlobalFoundries cooperated to build a new 12-inch factory in France to promote the construction of the FD-SOI ecosystem.
In addition, the chip factory jointly invested in by Sony and TSMC will also start production in 2024.
Advertisement
It can be seen that industry IDM chip giants are unanimously investing heavily with foundries to expand wafer factories. What exactly are they planning behind these actions, and what kind of industry trends are they revealing?
Behind the IDM and Wafer Foundry Alliance
IDM's Transition to Fablite
In the semiconductor industry, both wafer foundries and IDM companies have wafer factories.However, with the continuous advancement of semiconductor manufacturing processes and the accelerating pace of updates and iterations of semiconductor technology and products, IDM manufacturers face tremendous pressure in developing both products and production processes simultaneously.
At the same time, the wafer production lines of wafer foundry companies have swept through the chip design field. IDM companies, either to reduce costs or to consider product layout, have stopped production of some outdated wafer factory production lines and started to transform towards the Fablite model, that is, the light wafer factory model, outsourcing part of the manufacturing to foundries and only retaining a small part of the products for their own production.
Fablite is a strategy for companies to reduce investment risks and achieve "asset lightness." It combines the characteristics of IDM and outsourced wafer foundry. Under this model, related manufacturers or IDM companies retain part of their own production capacity, complete key production processes independently, and outsource non-key production process business to external processing to ensure the quality and reliability of chips, hence it is called the "light wafer" model. This model can provide a low-cost, more flexible solution for manufacturers who need to expand chip manufacturing capacity and respond quickly to market demand.
In the past few years, companies such as TI, NXP, Infineon, STMicroelectronics, Renesas Electronics, and ON Semiconductor have all had cases of selling wafer factories to optimize the company's operating conditions.
In the article "Analog Chips, at a Crossroads," the author mentioned, "With the changes in industrial development, IDM giants choose to outsource a considerable part of their production capacity to foundries, gradually moving from traditional analog IDM to the Fablite model."
In fact, as early as 10 years ago, the Fablite model had been proposed. According to data from IC Insights, in the five years before 2014, 72 wafer factories worldwide were closed, with 8-inch and 6-inch wafer factories accounting for as high as 65%, and 12-inch wafer factories accounting for 11%.
This means that the global semiconductor industry is unwilling to bear the huge pressure of production capacity and is moving towards Fablite.
At that time, European analog chip companies were ahead of the curve, such as NXP, STMicroelectronics, and Infineon, all of which started implementing the Fablite strategy earlier. For example, after NXP acquired Freescale in 2015, it rarely made other major acquisitions and instead continued to divest some businesses; STMicroelectronics and Infineon also outsourced part of their production capacity to foundries for the sake of maximizing profits.
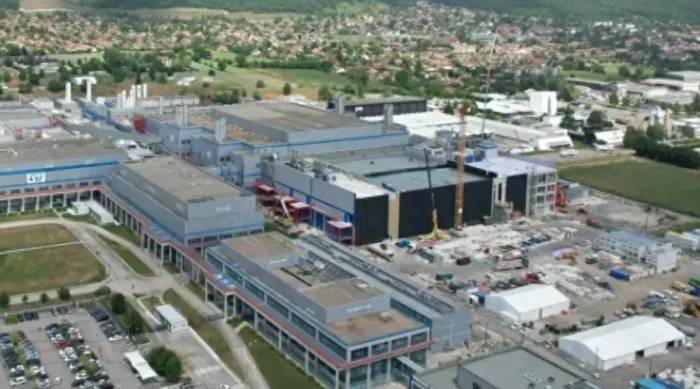
In the past few years, Japan has successively closed a large number of wafer factories. In 2022, Renesas Electronics closed its 6-inch wafer manufacturing factory in Yamaguchi Prefecture, Japan, transferring some capabilities to other 8-inch factories and discontinuing some products. In fact, in 2020, Renesas had already announced the closure of its 6-inch wafer factory in Kochi Prefecture.
Renesas's strategy is to continue investing in its own factories, but for advanced process nodes, it will choose to outsource to foundries such as TSMC, increasing the proportion of foundry/OSAT outsourcing.Onsemi is also transitioning from the traditional IDM model to a more flexible Fablite model. In recent years, Onsemi has sold its 200mm wafer fabs located in South Portland, Maine, Oudenaarde, Belgium, Pocatello, Idaho, and Niigata, Japan. At the same time, Onsemi is gradually exiting small-scale wafer fabs, shifting its focus to 300mm wafer capacity, and enhancing the flexibility of its general packaging backend factories, further increasing the external capacity from 34% in 2021 to about 45% in 2023.
A few years ago, ADI also initiated the Fablite model, retaining only some 6-inch and 8-inch fabs, while the acquired Maxim also chose to cooperate with foundries, starting to sell and reduce its own fabs, and the 300mm wafer is a model of jointly developing processes with foundries.
In addition, the IDM industry leader Intel is also outsourcing some of its business to TSMC. However, due to the constraints of its foundry process, on the one hand, while manufacturing for others, actively seeking customers, and competing with TSMC, it also needs to entrust TSMC with technologies such as 3nm. From the perspective of new product technology and process development, industry chain collaboration, and product delivery, it comprehensively enhances competitiveness.
It can be seen that almost all traditional IDM manufacturers are moving towards Fablite, becoming an evolutionary path in the development process of the semiconductor industry.
Regarding the IDM+outsourcing manufacturing strategy, an IDM manufacturer said: "Internal capacity is more for the delivery of differentiated products. For some standard production and packaging, we can fully utilize the advantages of outsourced suppliers. Through this operational model, we can provide customers with multiple sources while fully controlling the supply chain."
The advantage of the Fablite model lies in its flexibility and cost-effectiveness. It allows companies to flexibly adjust production scale and methods according to market demand and their own strategies, reducing fixed costs and risks through external cooperation. This model promotes technological cooperation and knowledge sharing, helping companies quickly adapt to market changes and accelerate technological innovation.
At the same time, the Fablite model can also help companies optimize investments, focus resources on core competencies and innovation, thereby enhancing market competitiveness and financial performance. Through this strategy, companies can effectively control costs and risks while maintaining technological leadership and market response speed.
Overall, against the backdrop of rapid development of the global economy and technology, the competition in the semiconductor industry is becoming increasingly fierce. The Fablite model can help companies achieve dual goals of technological innovation and cost-effectiveness, and strengthen their competitive position in the global market.
Wafer fabs have once again become "hot cakes".During the transition of IDM manufacturers to Fablite, wafer fabs were once regarded by some IDM companies as a kind of "burden".
However, since the end of 2019, the prolonged "chip shortage" and the frequent geopolitical conflict risks have led to a shortage of wafer manufacturing capacity, resulting in insufficient supply of products from many major chip manufacturers. This not only restricts the growth of revenue, but also affects cooperation with customers.
Under this background, wafer fabs have once again become the "hot cake" in the industry, with wafer foundries and IDM wafer fabs announcing expansion plans one after another. Even in 2023, a year of sluggish demand, there are still news of wafer fab expansion.
Even Fabless manufacturers have begun to build their own wafer fabs, showing the trend of developing towards the Fablite model.
At the end of last year, GCO's factory in the new area of Lin-gang, Shanghai, held a production ceremony, marking its complete transformation from Fabless to Fablite.
In addition, there are companies such as Zhuosheng Micro starting to build their own filter production; SiRui Pu starting to build their own test center; Shengbang Microelectronics has established a wholly-owned subsidiary to establish a test project, etc., and many domestic analog manufacturers are exploring the Fablite business model.
Secondly, under the influence of complex geopolitics, in the past two years, countries have introduced chip subsidy plans to build local semiconductor production lines. Among them, wafer foundries that can ensure the maximum wafer capacity are the focus of attraction for various countries.
Under this trend, the operating model of the semiconductor industry seems to be adjusting again, and many IDM manufacturers that previously adopted the Fablite model have begun to expand capacity, and some Fabless manufacturers have also started to build their own production plants to ensure a certain level of self-sufficiency, to ensure timely and safe supply of products in critical times.
This is also the reason why the transforming IDM manufacturers have started to focus on capacity supply again, and co-build capacity with wafer foundries.
· NXP & World AdvancedOn June 5th, NXP Semiconductors and the wafer foundry company World Advanced announced plans to establish a manufacturing joint venture, VSMC, in Singapore, where a new 300mm semiconductor wafer fabrication plant will be built.
The joint venture wafer fab will support mixed-signal, power management, and analog products ranging from 130nm to 40nm, targeting customers from the automotive, industrial, consumer, and mobile terminal markets. The foundational process technology is planned to be licensed and transferred to the joint venture from World Advanced. The joint venture is scheduled to begin construction of the wafer fab in the second half of 2024, with mass production expected to start in 2027. The joint venture will operate as an independent commercial wafer foundry supplier, providing guaranteed capacity ratios to both equity partners, with an expected monthly output of 55,000 300mm wafers by 2029.
Simultaneously, after the successful mass production of the first wafer fab, the partners will consider building a second wafer fab.
• ST collaborates with foundries to expand capacity
In 2021, STMicroelectronics and Tower Semiconductor, a leading global analog chip foundry, announced an agreement to jointly accelerate the capacity increase of the wafer fab, improve utilization rates, and reduce wafer costs. The two parties will share the R3 cleanroom, with TowerSemi installing its own equipment within one-third of the total factory space.
In 2022, GlobalFoundries and STMicroelectronics planned to invest several billion euros in a new 12-inch wafer fab in France, which will help Europe enhance FD-SOI and other chip manufacturing technologies and achieve capacity expansion goals.
The capacity target of the joint venture fab is 620,000 wafers per year, expected to achieve full production by 2026, with GlobalFoundries accounting for about 58% and STMicroelectronics about 42%. The manufacturing technology involves GlobalFoundries' FDX technology and STMicroelectronics' comprehensive technology developed for applications such as automotive, industrial, IoT, and communication infrastructure, ranging from 18nm.
The fab also becomes the second wafer foundry to benefit from the EU Chips Act subsidy program after Intel's new plant in Germany.
In June last year, STMicroelectronics announced that it would establish a new 8-inch silicon carbide device joint venture manufacturing plant with San'an Optoelectronics in Chongqing, China. The new SiC fab is planned to start production in the fourth quarter of 2025 and is expected to be fully operational by 2028, which will better support the growing demand for automotive electrification, industrial power, and energy applications in China.The joint venture factory will adopt STMicroelectronics' SiC patent manufacturing process technology, focusing on producing SiC devices for STMicroelectronics as a dedicated wafer foundry to meet the needs of its Chinese customers.
· TSMC & European Major Companies
In August 2023, TSMC announced that it will establish a joint venture with Bosch, Infineon, and NXP, with TSMC holding 70% of the shares and the other three companies holding 10% each. This is TSMC's first factory in Europe.
It is understood that TSMC's European semiconductor manufacturing company (ESMC) will start building a wafer factory in the second half of 2024 and begin production at the end of 2027, with a total investment estimated to exceed 10 billion euros.
It is reported that the wafer factory is expected to adopt TSMC's 28/22nm CMOS process and 16/12nm FinFET process technology, with a monthly production capacity of about 40,000 300mm wafers. The new factory will further strengthen the European semiconductor manufacturing ecosystem.
· Japanese Manufacturers Join Hands with TSMC
In 2021, TSMC and Sony invested $7 billion to establish a wafer factory in Japan, planning to supply chips to Japanese electronic equipment manufacturers and automotive companies.
This year, TSMC, Sony Semiconductor, Denso Corporation, and Toyota Motor announced further investment in TSMC's majority-owned wafer manufacturing subsidiary JASM in Kumamoto Prefecture, Japan, to build a second wafer factory and plan to start operations at the end of 2027.
The industry has stated that TSMC's second Japanese wafer factory will enter the 6nm and 7nm advanced processes. In addition to the previously invested Kumamoto Plant 1, the total investment in the two wafer factories will exceed $20 billion. In the future, the total monthly production capacity of JASM's Kumamoto wafer factory is expected to exceed 100,000 12-inch wafers.
In addition, automotive chip manufacturers such as Infineon, Renesas, Texas Instruments, and Rapidus are planning to start new wafer factory projects, with a total investment of up to $25 billion.Renesas Electronics also announced the commencement of operations at its Kofu factory located in Kai City, Yamanashi Prefecture, Japan, aiming to enhance the production capacity of power semiconductors to meet the growing demand for electric vehicles.
In addition, to ensure the security of production capacity supply, major industry players are also taking other measures in succession. For instance, Infineon has adopted a dual-factory strategy for some products, cooperating with TSMC to achieve mass production in factories in Taiwan and Germany, ensuring supply security. Furthermore, Infineon has implemented a new strategy known as "Secure Wafer Supply," providing a 12-week safety stock for qualified products, thereby further consolidating supply security.
NXP is also committed to ensuring localized resilience, providing high-quality products to customers locally and ensuring the corresponding infrastructure.
It can be seen that as the chip capacity shortage situation worsens in this round, and considering the controllable capacity under geopolitical factors, more and more IDM manufacturers are gradually building their own or co-building wafer production lines with wafer foundries, prioritizing capacity supply to achieve the effect of preventing minor issues from becoming major problems.
Industry chain manufacturers sign long-term contracts
On the other hand, due to the continuous shortage of wafer foundry capacity in the market, many major chip manufacturers have also signed long-term contracts with leading wafer foundries such as TSMC, UMC, and GlobalFoundries to ensure future capacity.
Similarly, for these top-tier wafer foundries, in order to ensure the stable supply and stable procurement prices of key raw materials required for production—such as semiconductor silicon wafers, photoresists, and other upstream materials, many have signed new long-term contracts with material suppliers.
Taking SiC as an example, Renesas Electronics announced a wafer supply agreement with Wolfspeed, a global leader in silicon carbide technology. Renesas Electronics will deliver a deposit of $2 billion to ensure a 10-year supply commitment of Wolfspeed's silicon carbide bare wafers and epitaxial wafers. The supply of high-quality silicon carbide wafers from Wolfspeed paves the way for the large-scale production of silicon carbide power semiconductors by Renesas Electronics starting in 2025.
From the manufacturing end, signing long-term contracts can ensure stable supply and balanced prices for the coming years.An increasing number of manufacturers in various fields of the semiconductor supply chain are beginning to sign agreements. Fabless chip design companies are starting to tie up with wafer fabs and bind with upstream material manufacturers. After experiencing the baptism of "chip shortage," downstream automotive companies have also begun to closely couple with chip design enterprises.
Under various trends and directions, it is not difficult to understand the purpose of IDM manufacturers and wafer foundries jointly building production capacity.
They all reflect that the global chip shortage has led all manufacturers to re-examine the problems in the traditional supply chain. This strong coupling and customized cooperative relationship between semiconductor companies and the upstream and downstream of the supply chain has become a trend, which may gradually become a business model in the semiconductor industry in the future. It aims to help companies obtain sufficient capacity allocation in the next few years and avoid the passive situation of chip shortage.
In conclusion, whether it is the streamlining of IDM manufacturers to the Fablite model, the construction of new wafer production lines by Fabless, or the recent joint construction measures between IDM companies and wafer fabs, it all illustrates the importance of manufacturing for chips.
In the semiconductor field, vertical integration still has great practical significance. At the same time, adopting a flexible and appropriate manufacturing and distribution model is also a problem that IDM chip companies must consider comprehensively to ensure competitiveness.
In the final analysis, the choice of which business model cannot be generalized. Manufacturers in the industry chain need to make a comprehensive assessment based on various factors such as industry attributes, the strengths and weaknesses of the company itself, market environment, and strategic planning, and choose a model suitable for current development is the best.
Comments