In June 1993, Samsung Chairman Lee Kun-hee proposed the "New Management" declaration in Frankfurt, Germany, which had the greatest impact with the famous saying, "Everything must change except for your wife and children." Although Samsung had just taken the first place in the DRAM market at that time, the rest of Samsung's departments were not as successful as the semiconductor industry. Outside of South Korea, products labeled "SAMSUNG" were usually second or third-tier products that no one cared about.
To demonstrate Samsung's determination, in March 1995, more than 2,000 employees of Samsung Electronics gathered on the playground of the Gumi factory area, where Anycall mobile phones were piled up like mountains. Everyone wore a cloth band on their heads with the words "Ensure Quality" written on it. In the end, 150,000 mobile phones with a total value of 50 billion won were smashed with hammers and burned.
In the 1980s, Samsung Group was once lagging behind LG and Hyundai. As the second-generation leader of Samsung, Lee Kun-hee reshaped the Samsung Empire with strong means and foresight. Among them, the semiconductor and mobile phone departments were the focus of his attention, and they successfully made a name for themselves in the 1990s, becoming the two most important pillar industries of Samsung.
Advertisement
More than thirty years have passed since Lee Kun-hee made the Frankfurt declaration, and now Samsung is troubled, with a pile of problems. The first financial group in Korea seems to have lost its spirit at that time.
The market is hard to hide the downturn.
On the 31st anniversary of Lee Kun-hee's declaration, the current chairman of Samsung, Lee Jae-yong, also went to the United States on a business trip, just like Chairman Lee Kun-hee traveling around the world at that time. Lee Jae-yong also completed more than 30 official schedules in various parts of the United States within two weeks. Although compared with the period of the new management declaration, Samsung has developed into a larger and better enterprise, the reality faced by Lee Jae-yong is still not optimistic.
According to the data from Eugene Investment Securities, Samsung Electronics' sales volume has only increased by an average annual rate of 2.3% from 2012 to 2023, 11 years after breaking through 200 trillion won. In US dollar terms, the growth rate is only 1%, which is a very bleak report card, and it has not even kept up with the growth rate of South Korea's GDP.
This is just a rough look. When we take a closer look at the current performance of Samsung Electronics, we will find a bigger problem. In 2013, the sales volume of Samsung Electronics' mobile department was equivalent to 73% of Apple's sales volume, but by 2023, this figure not only did not increase but also fell sharply to 22%. The Galaxy S and Note series once competed with the iPhone in sales volume. The Galaxy S4 alone sold 70 million units, but now the total sales volume of the three Galaxy S23 phones is only just over 30 million.
What about Samsung's semiconductors? First, let's look at the non-memory department. The sales volume of this department was 88% of TSMC in 2011, but by 2023, it fell to 26%. In 2019, Lee Jae-yong announced the grand plan of the "System Semiconductor 2030 Vision," planning to invest 133 trillion won by 2030, and to be the first in the field of system semiconductors such as design (Fabless) and foundry (Foundry). However, four years later today, the gap between Samsung and TSMC has not only not narrowed but has expanded.According to TrendForce data, in 2019 when Samsung announced its vision for system semiconductors, TSMC held a market share of 51.8%, while Samsung had 18.5%, a gap of 33.3 percentage points. However, in the fourth quarter of 2023 in the global foundry market, TSMC's market share was 61.2%, and Samsung's share was 11.3%, widening the gap to 49.9 percentage points.
The more fatal issue is the core business of the rise of the Samsung Empire—memory semiconductors. Since 1993, Samsung has been firmly in the first place in the memory fields such as DRAM and NAND Flash, but now it is facing difficulties in producing High Bandwidth Memory (HBM) used for artificial intelligence (AI) semiconductors.
It is now July 2024, more than a year and a half since the AI craze, and more than a year since Nvidia ascended to a market value of a trillion dollars, but Samsung has not yet embraced Nvidia's thigh. In June this year, in response to questions about the HBM used in his company's AI accelerators, Nvidia CEO Huang Renxun said: "Samsung Electronics, SK Hynix, and Micron will all supply HBM to Nvidia," "We are also working to arrange (Samsung Electronics, Micron) to pass the test as soon as possible and be put into the use of AI semiconductor processes."
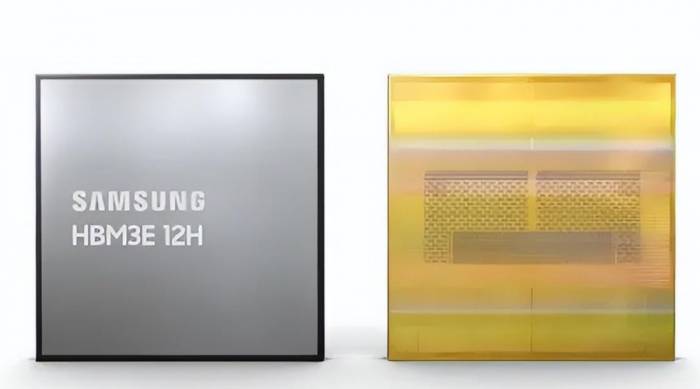
Passing the test as soon as possible, that is to say, so far, Samsung has not officially supplied HBM to Nvidia. In response to recent reports that Samsung Electronics' HBM failed the test due to heat issues, Huang Renxun also responded: "That is not the reason for failure, such reports are not worth mentioning," "The cooperation with Samsung is progressing smoothly, I wanted to finish it yesterday, but it was not successful, patience is needed."
From Nvidia's perspective, the more suppliers of HBM, the better. Currently, SK Hynix's exclusive supply of HBM only leads to uncertainty and also results in insufficient bargaining power. Although it has the intention to introduce Samsung and Micron, the two companies are still striving to pass the quality test, becoming a helpless Ah Dou.
As the third in the industry, Micron's misjudgment of the technical route to its own HMC standard, leading to a lag in the progress of HBM, is understandable. As the leader in DRAM, Samsung once served as the exclusive supplier of Nvidia's HBM, but now it cannot even meet the standards of AI products, which is really a bit sad.
In fact, since 2015, Samsung has been actively investing in the development of HBM and has successfully completed the first large-scale production of commercialized HBM products, defeating Hynix in the third-generation product HBM2E. However, in 2019, due to the slow growth of market demand, Samsung reduced its investment in HBM and downsized the team.
Samsung Semiconductor underwent a business reorganization in July this year, and the two dedicated HBM development teams operating in the form of task forces were incorporated into the DRAM development department of the memory business division, reorganized into a new HBM development team. This change is one of Samsung's important measures to narrow the gap with Hynix in HBM.
However, the problems that Samsung needs to deal with now are far more than just HBM.Internal Conflict Escalates
Many may have heard before that the Samsung Electronics labor union recently held a major strike. It is worth noting that this is the first time in 55 years since the establishment of the Samsung labor union.
On June 7th of this year, the National Samsung Electronics Labor Union (hereinafter referred to as "Quan San Labor") conducted a vacation struggle through collective leave. On July 8th, Quan San Labor held a general strike resolution meeting in front of the Samsung Electronics Hwaseong Business Center in Hwaseong City, Gyeonggi Province, with a plan to strike for two days. The main demands are to increase members' wages, increase vacation time, and improve the performance bonus system.
Quan San Labor has about 30,000 members, accounting for 24% of all Samsung Electronics employees (about 125,000 people). As of 11 am on the 8th, Quan San Labor said that a total of 6,540 union members participated in the strike. The Gyeonggi Dongtan Police estimated that the number of people gathered that day was about 3,000. Subsequently, because Samsung's management did not attempt any dialogue during the strike, Quan San Labor announced an upgrade to an indefinite general strike on July 10th.
Before Lee Jae-yong officially announced the abolition of the non-union operation policy in May 2020, Samsung Group has long pursued a "non-union operation." This logic believes that for employees, providing generous treatment can be done without a union; for the company, it can achieve more efficient operation. However, this approach has always been criticized for infringing on labor rights.
Quan San Labor was established in November 2019 as an organization under the Korean Labor General Federation National Metal Labor Union (hereinafter referred to as "Metal Labor Union"). Most of its members are affiliated with the Device Solutions Department (DS) responsible for semiconductor business, which has the largest number of members among the five labor unions of Samsung Electronics. However, due to not reaching half of all employees, the bargaining power is limited.
Quan San Labor Committee Chairman Sun Yu Mu said in an interview with BBC Korea: "In the past, Samsung's logic was that there would be rewards as long as there were achievements, but now even with achievements, the rewards are only given to executives, and employees do not have them." Sun Yu Mu added, "It is normal for employees not to receive performance bonuses if the company is at a loss, but we demand a public and transparent standard."
At present, the proportion of performance bonuses in Samsung employees' wages is relatively high, but the calculation standard is unclear, leading to great uncertainty. The union is dissatisfied with the fact that last year, due to the loss of Samsung Electronics' semiconductor department, employees could not receive performance bonuses equivalent to more than 50% of the basic salary, while executives received bonuses under other names.
In addition, one point worth noting about Samsung's strike is the improvement of the working environment. The focus of Quan San Labor's second strike was on the Samsung Electronics Qi Xing factory, which has an 8-inch wafer production line for producing traditional semiconductors for automotive and home appliances. Most of Samsung's 12-inch production lines are equipped with automated equipment, that is, overhead crane transporters, which can transport bundles of wafers from the factory's ceiling, while this old 8-inch production line still relies on manual handling.On July 13th, the sixth day of the total strike at Samsung Electronics' factory in Gyeonggi, participants shared a photo of a finger with a prominent knuckle in their KakaoTalk group chat, accompanied by the message "The finger is deformed." This picture sparked comments like "You can see the '8-inch' production line's medal just by looking at the finger," and the group chat was soon filled with other images and testimonies about varicose veins, plantar fasciitis, lumbar disc herniation, and cervical disc herniation. Through the group chat, workers shared their experiences of high-intensity labor and unreasonable treatment, and expressed that "this time it must change."
According to the data from the All-Samsung Labor Union, on the first day of the strike, the operation rate of Samsung's 8-inch production line dropped from 80% to 18%. Most of the active participants in the strike are female workers aged 20 to 40, who hope for more than just "salary increases" and "additional holidays"; they want to be treated as human beings, not as parts.
It is understood that while most of the 12-inch production lines have been equipped with automated devices, workers at the 8-inch production line of Samsung Electronics' factory in Gyeonggi still need to manually carry semiconductor silicon wafers weighing 3 to 5 kilograms. This production line operates 24 hours a day, 365 days a year, divided into three shifts at 6 am, 2 pm, and 10 pm. Workers are required to stand for 8 hours a day, manually carrying and operating these silicon wafers, which has led to diseases such as finger deformities, varicose veins, and lumbar disc herniation due to high-intensity labor.
Although there is an hour for meal breaks among the workers, the machines keep running, and someone else must take over the work, making it impossible for them to eat or use the restroom in peace. A worker who has worked for 25 years said, "To avoid severe cystitis, I dare not drink water or touch coffee before going to work."
For shift workers who work day and night, rest is essential. However, due to a shortage of personnel, holidays are not taken seriously. "Other departments say that the statutory annual leave must be used up, but I have to climb high to arrange for annual leave," said a worker who joined Samsung in 2010, mainly working on the 8-inch production line. "Even if new employees come in, they often leave because they cannot adapt to the shift work, so there is always a shortage of personnel. When more people want to take annual leave, we have to play the game of rock-paper-scissors. You have to win the game of rock-paper-scissors to be able to use your annual leave."
In fact, Samsung's factory in Gyeonggi is not the first time it has been reported by major Korean media. As early as 2007, a 22-year-old Korean girl named Hwang Yu-mi entered Samsung's factory in Gyeonggi, responsible for semiconductor cleaning work, and died of leukemia less than two years later. Her father discovered during the rights protection process that due to exposure to highly toxic raw materials, 320 people in the factory had fallen ill, and 118 had died. This incident caused a strong reaction in South Korea and was adapted into the movie "Another Promise." It was not until 2018 that Samsung officially apologized to these cancer-stricken workers. Hwang Yu-mi's father, Hwang Sang-gi, has said many times: "If Samsung had a labor union, my Yu-mi would not have fallen ill or died."
In response to these allegations, Samsung Electronics still completely denies them. A person in charge of Samsung Electronics responded, "When employees apply for work-related injuries, we will actively support them." He also said, "For accidents that require more than 4 days of rest or work stoppage, we will guide the application for work-related injuries, so the statement that applying for work-related injuries will be adversely affected is completely unfounded." He added, "Every year, we will conduct training on the work injury process guide for statutory management supervisors, and conduct regular checks on musculoskeletal burden operations every three years."
He stated that Samsung strictly complies with the working environment standards of the Industrial Safety and Health Law and emphasized that the strike did not affect production performance. Measures will be taken in the future to prevent the occurrence of problems.In stark contrast to Samsung, the neighboring competitor SK Hynix has not encountered large-scale strikes in its more than twenty years of establishment. After the merger in 1999, Hynix fell into a predicament. Unlike Samsung Electronics, which covers semiconductors, mobile phones, home appliances, displays, and other businesses, Hynix had no support to rely on in the semiconductor industry and could only struggle to save itself by fighting with creditors. This situation has promoted unity between Hynix's labor union and the company.
During difficult times, the Hynix labor union participated in overcoming the crisis through wage freezes and collectively agreed upon agreements without negotiation. The company did not carry out layoffs and overcame difficulties together with its employees. The Hynix labor union also pioneered the "wage-sharing model," where a portion of the increased employee wages during profitable times is used to support partner companies.
Of course, the above part is all old news. In fact, Hynix also encountered problems similar to Samsung in the past two years. In February 2021, in response to the strong dissatisfaction of executives and employees who received performance bonuses lower than expected and demanded improvements in the measurement criteria, SK Hynix held a labor-management meeting. Both parties reached a consensus on abolishing the EVA (Economic Value Added, a figure obtained by deducting various costs such as corporate taxes from operating profits) system, and the performance bonus was changed to be based on 10% of the operating profit.
At the same time, the chairman of SK Group, Chey Tae-won, took the lead in announcing that he would return his salary from Hynix. Hynix CEO Lee Seok-hee also issued a statement explaining the situation, and their approach to solving problems has become an example of resolving labor-management relations in South Korea in recent years.
Looking back at Samsung's handling of the situation, it is somewhat embarrassing. After Lee Kun-hee's death and Lee Jae-yong's succession, the problems of this huge empire have concentrated and erupted, and solving them is by no means easy. Relying on emergency changes in leadership is just a temporary measure to provide psychological comfort to the outside world.
In conclusion, in 2010, Lee Kun-hee said, "Most of the products and businesses that Samsung is launching today will disappear within 10 years. We should start over, and there is no time to waste." Even when Samsung's mobile phone shipments set a new record in 2013, Lee Kun-hee still called for change: "We must promote innovation with greater intensity and lead the industry trend."
For the semiconductor market, there is no eternal overlord. Having experienced Samsung's low point and witnessed the rise and fall of hundreds of domestic and foreign companies, Lee Kun-hee, who played a key role in the growth and development of Samsung's semiconductors and smartphones, is very clear about this point and is always worried about the future of this commercial empire.
Now, Samsung, plagued by various problems, would not want to have a major transformation like that of 1993?
Comments